An automotive parts supplier uses an integrated dry ice blasting system to completely automate their burr removal process.
A global automotive parts supplier set an ambitious plan for their newly built facility in China - to establish a completely unmanned factory for the production of electric driving components.
The Problem
“We use an ultrasonic welding process to attach two components together in order to create a perfect air-tight chamber for the rotor,” said the Director of Project for the automotive parts supplier. “Inevitably there will be some burrs around the welded cap and that needs to be removed. After deburring, we blow inert gas into these parts to check the airtightness. Any leakage is unacceptable. Traditional automated deburring methods can hurt the seal and we do not want to do this by hand.”
Condensate water is a major concern for the company. All of the ventilation and heating customizations are crucial and condensate water must be excluded as it may affect the airtightness test result. The company also needed a solution that would be capable of running 24/7.
The parts supplier decided to use dry ice blasting to remove the burrs. Dry ice blasting, also called dry ice cleaning, is an environmentally responsible cleaning, surface preparation, and parts finishing technique. Dry ice blasting uses solid carbon dioxide (CO2) pellets or MicroParticles, which are blasted at supersonic speeds and sublimate on impact, lifting dirt and contaminants off the underlying substrate as well as removing flash and burrs from parts. Dry ice blasting is non-abrasive, non-conductive, non-toxic, and non-flammable.
Dry ice blasting can easily remove the burrs from the components, but it would take more than a dry ice blaster to meet their needs.
Learn more about dry ice blasting.
The Solution
The COMBI 120H is an unmatched solution in this application. The COMBI 120H is an automated system that combines dry ice pellet production with dry ice blasting. This automated solution allows for dry ice blasting equipment to be integrated within a production line via a robotic system. The automated system is equipped with a pelletizer unit that guarantees continuous cleaning with freshly made dry ice. The automated system is placed in a sound reduction chamber that allows for the control of noise as well as the extraction and filtering of air.
Integrated dry ice blasting systems are cost effective solutions that provide superior cleaning performance and minimal space requirements. The systems enable continuous, uninterrupted, and fully automated operation.
The COMBI 120H and its accessories have been developed with the intention of manufacturing an automated cleaning system which both meets the requirements of industrial companies for a continuous cleaning process, and minimizes consequential costs of machine / plant cleaning and maintenance.
Moreover, a small chamber is designed by Cold Jet engineers to contain the components while blasting. All the residues are collected by ventilators attached on the opposite side of nozzle. Heating units are installed on a series of positions including blasting chamber, nozzle, and clamping platform. Hot air is blowing onto the components to evaporate the last drop of condensate water. The whole process is 100% dry.
“The COMBI 120H helps us fulfill the requirement of our unmanned factory,” said the Director of Project. “It does not hurt the airtightness of our products like traditional deburring methods. This task cannot be done otherwise.“
The Results
Cold Jet’s COMBI 120H has made it almost impossible to damage products during deburring. The rejection rate is reduced from 1% to 0.1%.
Not only did the company reduce their rejection rate, but they also reduced the amount of labor needed.
“Labor cost is significantly reduced,” said said the Director of Project. “It took eight workers in another plant to finish the same process, now there is only one person taking care the whole line. At the same time, the safety of the workers has been increased and the process is environmentally friendly.”
The Director of Project was sure that given their success that the integrated dry ice blasting process would be used at other company facilities.
“Because of the savings in both time and costs, I am sure these systems will be used at other plants,” said the Director of Project. “They allow for a significant increase in process reliability and have helped us to maintain our high-quality standards.”
The facility plans to add a second production line and will implement the integrated dry ice blasting system on that line as well.
“The second production line is under construction,” said the Director of Project. “Thanks to the savings in time and costs, I am sure that this system will be used on the second line as well. It allows for a significant increase in process reliability and have helped us to maintain our high quality standards.”
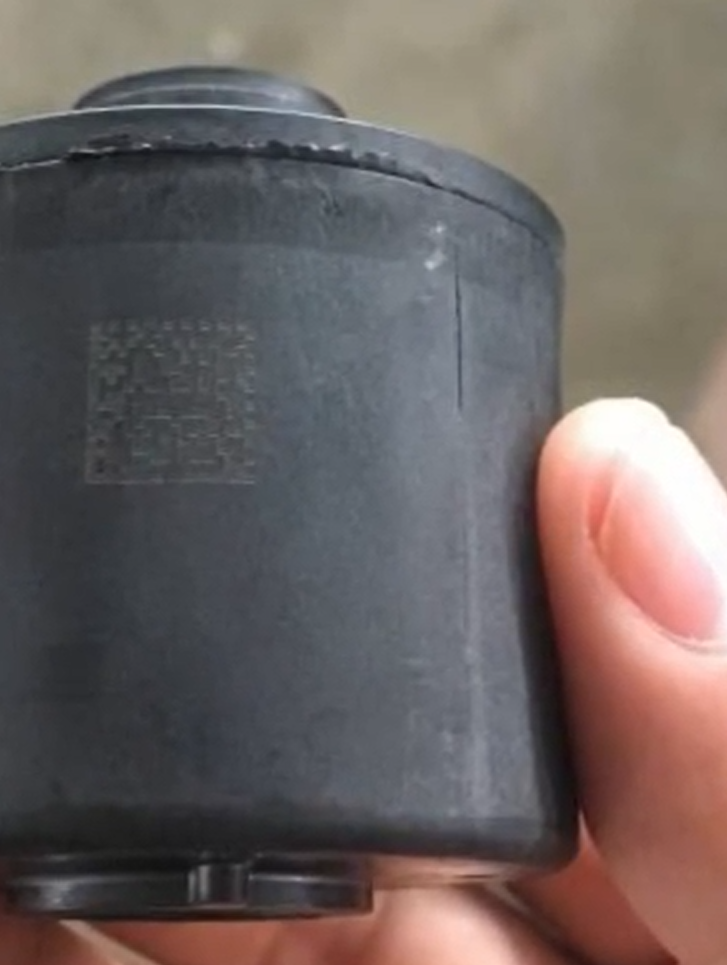